Weld seam machining with professional tools – from the preparation to a mirror finish with LUKAS
The finishing quality of weld seams is crucial to ensuring the functionality, durability, reliability and appearance of welded metal parts. Weak points such as splashes, burrs or sharp edges can be removed before they can result in stress fractures or breakages.
In the food and beverage industry in particular, a professionally smoothly ground seam on stainless steel or aluminium parts is crucial for preventing corrosion caused by moisture and dirt ingress. The visual appearance is also an important factor in the automotive, aviation and construction industries. Smooth, evenly ground surfaces are not only aesthetically appealing, but also testify to high-quality workmanship. In the case of surface coatings such as paint, electroplating or powder coatings, weld seams must also be smooth and clean to prevent premature flaking due to uneven surfaces or impurities.
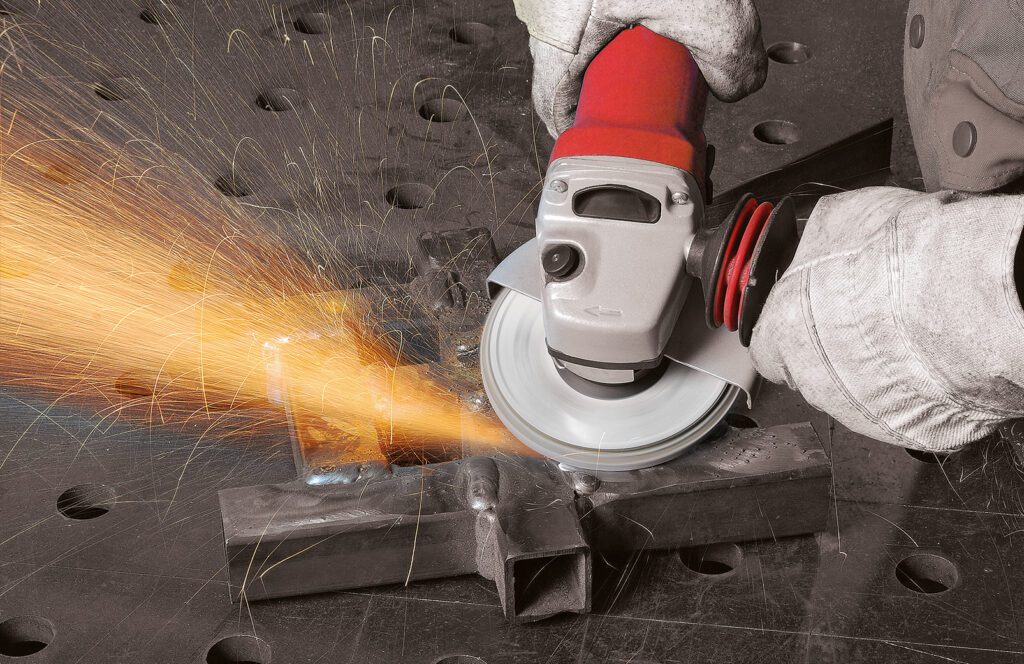
On account of its durability and resistance to corrosion and heat, stainless steel is often used for high-performance applications such as medical furnishings, aviation equipment and commercial kitchens. The chemical, medical, food and beverage industries require shiny and fine surfaces as these signalise and guarantee visual cleanliness and adherence to hygiene standards. Weld seam machining is therefore a critical process which ensures that the surface quality fulfils the demanding requirements of these industries. The problem with weld seams lies in the need for a smooth and homogeneous finish, not only to avoid structural weaknesses, but also to fulfil aesthetic and hygiene standards. Defects such as pores, cracks or uneven surfaces can impair the functionality of the welded joint and must therefore be carefully machined.
Specialist tools are essential for all kinds of weld seam machining in order to ensure high-quality joints. LUKAS-ERZETT offers a broad assortment of tools that have been developed for the coarse and fine machining of weld seams and are designed to work efficiently. One example is the LUKAS SLTT lamellar flap disc, which enables especially high removal rates thanks to its patented sickle flap shape and state-of-the-art abrasive cloth. These grinding discs are ideal for chamfering edges, grinding out weld seams and eliminating surface irregularities. Chamfering creates space for weld seams and makes subsequent welding easier, while the grinding ensures an even seam surface.
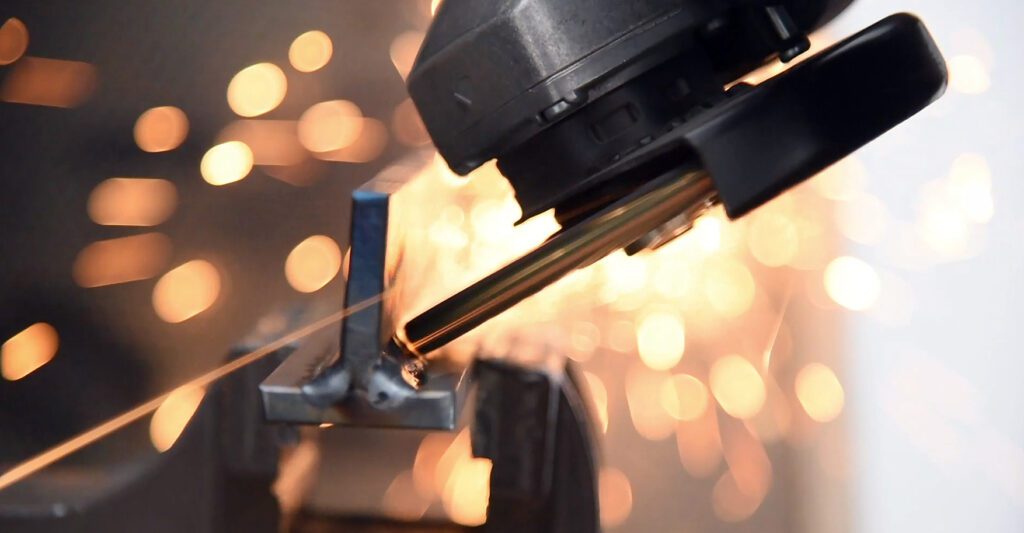
With the U-Edge Pro, LUKAS has once again demonstrated its innovation prowess. The U-Edge Pro is more than just a grinding tool – it is an innovation in grinding technology that will satisfy the most demanding requirements. Its unique design enables effective grinding that leaves conventional tools far behind. Perfect precision for fillet welds: Machining fillet welds requires an extreme level of precision and efficiency. Its unique design enables highly precise machining of fillet welds on both small services and difficult-to-reach areas. Thanks to its U-shaped edge, the U-Edge Pro can adjust effortlessly to both small and large radii and the contours of weld seams.
It therefore delivers precise and reliable results even in the tiniest spaces, boasting greater ergonomics, effectiveness and precision than any other grinding disc! The U-Edge Pro offers a broad range of possible applications for weld seam machining. From grinding fillet and repair welds to cleaning, paint stripping and making visual improvements – the radial abrasive surface of the U-Edge Pro makes it the perfect all-rounder for achieving precise and efficient weld machining results.
LUKAS also has the right tool for the toughest and most sustained applications in weld seam machining: the LUKAS V2 Power Heavy Duty lamellar flap disc. The V2 Power Heavy Duty is especially robust even when machining edges, tempered steels, scale surfaces, titanium, stainless steel, hard coatings and reinforced weld seams. The innovative dual combination of self-sharpening ceramic abrasive grain and the multi-layer abrasive coating with the LUKAS patented sickle flap shape enables consistent performance levels throughout the entire duration of the work from the first time it is used. Deburring, fettling, derusting and smoothening work or weld seam machining always succeed with perfect sharpness thanks to the self-sharpening effect of the ceramic grain. During use, blunt ceramic particles repeatedly break off and expose new particles with fresh, sharp cutting edges, meaning that tool changes are required much less frequently and tool costs are reduced.
Stainless steel surfaces in the food and beverage industry must not only be clean and shiny, but also have to be resistant to chemical cleaning agents and mechanical stress. LUKAS tools have been specially developed for requirements such as these and guarantee a flawless surface quality that meets the highest hygiene standards, as impeccably smooth and hygienic surfaces are a must in industries such as the catering and medical technology sectors. Not only is the structural strength of the weld seams important in such applications, but also the aesthetic appearance and compliance with strict hygiene standards. LUKAS offers special tools for this purpose, which enable surface finishing up to a mirror finish.
Precise tools are required to machine weld seams to match the surrounding surface through to the polishing. Shiny or satin-matt surfaces that fulfil both visual and hygienic requirements can be achieved with the high-quality grinding and polishing tools from LUKAS.
The simple way to create an absolutely perfect surface finish for medical furnishings and stainless steel kitchens, for instance. The P6PT polishing discs from LUKAS enable you to achieve the desired polishing results, from rust to a mirror finish, quickly and easily. A standard adjustable angle grinder is the perfect basic tool for working with these polishing discs. The lightweight, stable and flexible design of the P6PT polishing disc series delivers outstanding surface results. Hard materials can be effortlessly and efficiently machined with these polishing discs as the hard and sharp abrasive grain of the four discs with grit sizes P150, 240, 400 and 800 ensures a long tool life when cleaning, grinding or polishing surfaces. Thanks to the cool grinding and absence of sparking, these LUKAS silicon carbide polishing discs are even approved for use in aerospace engineering. The disc is highly resistant to breakage and generates little vibration when working. Combined with its easy handling, it is ideal for manual use.
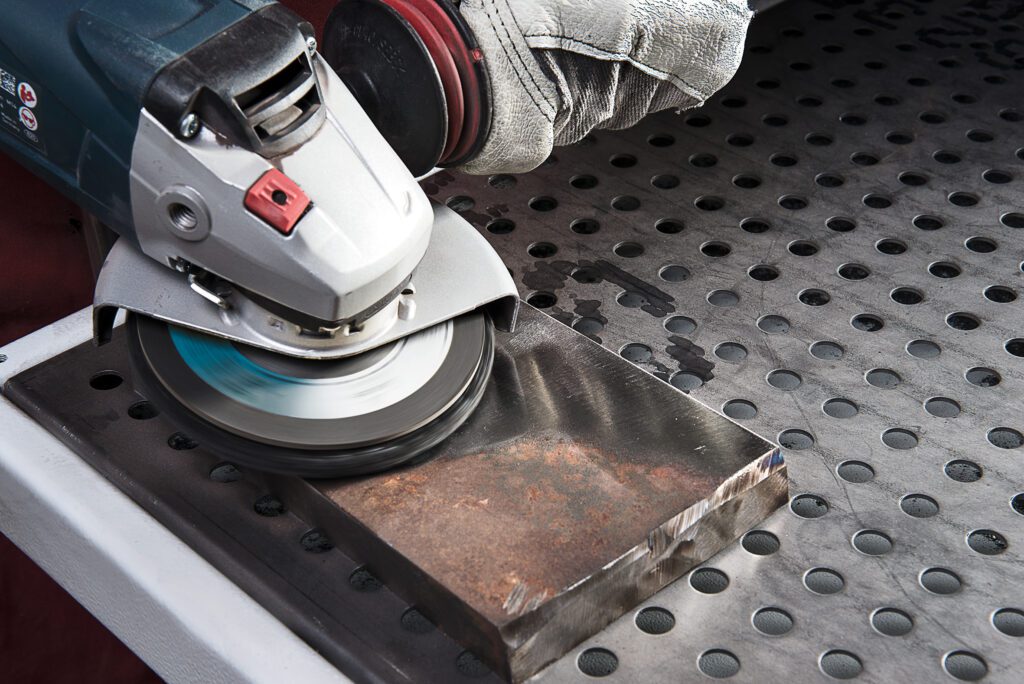
Particularly in industries with such challenging surface finish requirements, it is vital to also treat hard-to-reach areas with the same diligence and attention. LUKAS also offers an optimised tool for such applications: the extremely flexible SLTs-flex flap disc ,Ø 125 mm with zirconia alumina grain 60, flat with sickle-shaped flaps, is the perfect alternative to rough grinding discs or standard flap discs when machining hard-to-reach areas. Deburring, fettling, derusting and smoothening work or weld seam machining always succeed with perfect sharpness thanks to the self-sharpening effect of the ceramic grain. Thanks to the even larger flap overlap than the SLT-flex and the small resin core with its practical M14 thread, this grinding disc offers maximum flexibility, adapts itself to uneven surfaces and requires little effort when working. Compared to grinding discs, the LUKAS patented flap shape and arrangement provides for 50% lower noise levels, less vibration, faster operation, greater efficiency and better surface results.
Products from LUKAS-ERZETT are a byword for pioneering innovations in the tool industry. As a technological leader for milling, grinding, polishing and cutting system solutions, the experts at LUKAS-ERZETT GmbH & Co. KG work tirelessly to develop products of the highest quality, performance and reliability. With its broad range of applications and impressive performance, the company sets standards in grinding technology and offers professional solutions for all grinding tasks from rough machining through to achieving the perfect finish.