Capable of handling any shape in 3D printing: Perfect finishing with LUKAS tools
NEXT LEVEL 3D PRINTING. LUKAS is the tool partner for additive manufacturing processes.
3D printing, also called additive manufacturing, has already found its way into many areas and sectors of industry and is undergoing constant further development. The process gives companies and developers the freedom to create shapes that could never have been produced using conventional manufacturing methods. In the construction of demonstration and functional prototypes, for small and medium-sized series production runs, and increasingly for large-scale series production runs, this innovative manufacturing process convinces with advantages that can only seldom be achieved using conventional production technologies.
The professional production process is consequently becoming increasingly important for many different markets and still holds much potential for the future. Many different materials are already being used for manufacturing parts and components such as various metals, plastics and composites, but also ceramics and other materials.
Small series production runs with manual challenges
Many different workpieces are, for the most part, still being produced by service providers (as it is not yet worthwhile to purchase a proprietary 3D printer, for example) or by the manufacturers themselves in small series runs. However, only in the rarest cases do workpieces and manufactured parts come out of the 3D printer ready for use. All kinds of factors require finishing work on the parts, as Dr Gerd Fischer, head of the development department at LUKAS, explains here in more detail: “Parts manufactured with the aid of additive manufacturing are often extremely dependent on supporting structures. This is the only way to build up parts layer by layer in the powder. However, these supporting structures must be removed afterwards so as not to impair the functionality of the workpiece.” This usually requires the time-consuming manual use of tools.
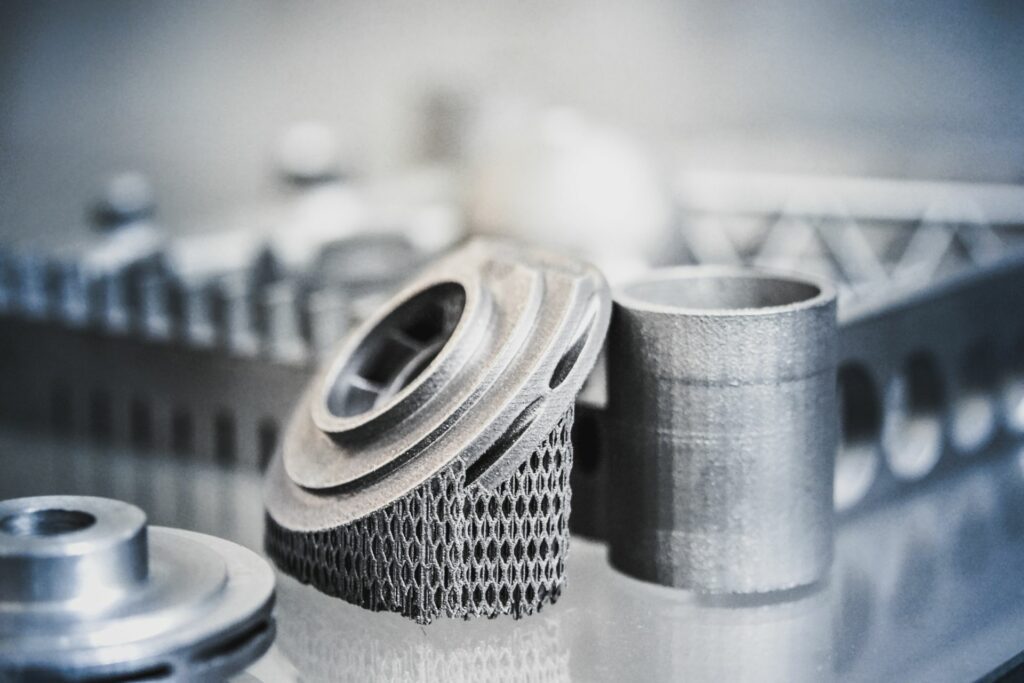
But that is not all: “Smoothening surfaces, for example for removing stepping effects from bevels and radii, producing flat surfaces or cleaning bores and the concluding polishing, also require a lot of manual work and tools that are as flexible as possible, yet still precise,” continues the LUKAS Head of Development. “The manifold possibilities of 3D printing offer many opportunities, but also pose a challenge for the necessary finishing of the parts. We at LUKAS can offer effective help to 3D printing users and make their work easier.”
LUKAS as a finishing problem-solver
As an internationally operating tool manufacturer with over 80 years’ experience, LUKAS has everything it takes to support additive manufacturing processes. LUKAS has made a name for itself as a problem-solver in many different industries, such as the automotive and aerospace industries, and is the specialist for innovative solutions and the manufacture of high-performance tools with customers worldwide.
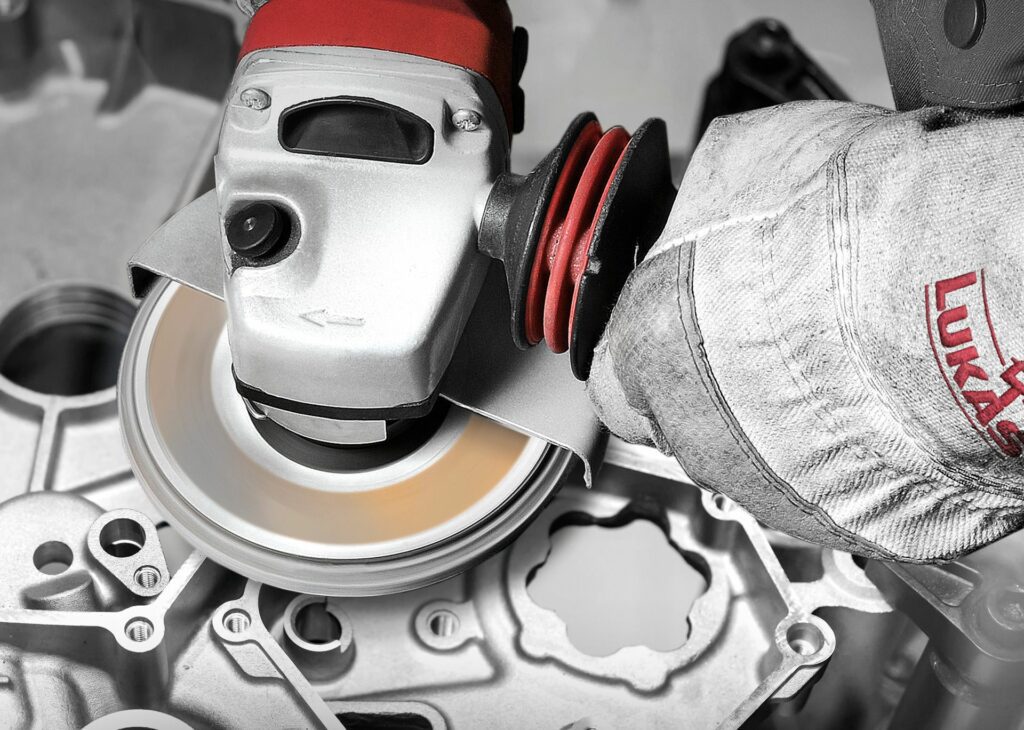
Georg Klug, in charge of product management at LUKAS, is certain that the LUKAS tool range is ideally positioned for finishing 3D printing products of all types and shapes – regardless of the material: “With mounted points, polishing points and burrs from LUKAS designed for universal use, we can offer optimum support to companies in the additive manufacturing sector.” The extensive standard product range of tool manufacturer LUKAS comprises almost 3,500 articles and includes ideally suited tools for finishing workpieces. “In particular, our 3D printing burr series with its specially developed geometries and a specifically optimised toothing allows supporting structures to be easily removed and cut off as precisely as with a scalpel,” explains Georg Klug. “This means that we save the user time, effort and unnecessary work steps during the manual finishing.”
Cooperations with renowned 3D printing companies for individual solutions
If a user’s problems cannot be fixed with a standard solution from LUKAS, the head of product management believes that the innovative tool manufacturer is well prepared: “Our technicians come directly from practical fields and have many years of in-depth user, production and industry knowledge. In addition, we collaborate directly with renowned 3D printing companies to optimise our tools even further for this specific application. We bring this knowledge straight to you and together we work out an individual solution.”
Users of 3D printing processes are therefore in the best hands with LUKAS and are given every possibility for systematically streamlining their finishing processes. In this way, LUKAS enables manufacturers to optimise their time-to-market and to supply their own customers with ideal solutions in a cost- and time-efficient manner.
About LUKAS:
LUKAS – NEXT LEVEL SOLUTIONS.
As a technologically leading manufacturer of powerful and innovative milling, grinding, polishing and cutting tool solutions, LUKAS-ERZETT GmbH & Co. KG, based in the greater Cologne area, always focuses on the requirements of its customers and the latest developments in many different industries. AGILE, SUSTAINABLE, RELIABLE and FUTURE-ORIENTED – LUKAS thinks further, develops tailor-made solutions, and is always one step ahead of market requirements. This focus gave us the lead early on in the market and still does to this day.
All of the products that we manufacture and sell stand for outstanding quality characteristics such as powerful working, a long service life, excellent ergonomics and the very best results. If standard solutions don’t suit, we develop customised solutions to satisfy every application. This way, both your products and ours will always be ready for whatever the future holds.
LUKAS at the cutting edge of a global industry
With around 700 employees, state-of-the-art production sites in Germany, the Czech Republic and South Africa, a huge wealth of experience and a broad product range, LUKAS is firmly established in the markets. We are internationally active with branches and representatives on every continent. With over 80 years of experience, we produce system solutions for use in the automotive, aerospace, energy and construction industries, as well as for tradespeople.