The expert for 3D-printing finishing
Next Level Solutions for additive manufacturing with LUKAS-ERZETT
Additive manufacturing processes are innovative and future-oriented production methods that have long since made the transition from the garages of DIY tinkerers into the production halls of internationally operating corporations.
The principle of an additive, layer-by-layer construction method for assemblies offers the user undreamt freedom of design that would have been absolutely impossible using conventional subtractive manufacturing methods. The professional production process is consequently becoming increasingly important for many different markets and still holds much potential for the future.
Additive processes also have the potential for achieving enormous time and cost savings, in particular in the field of model and prototype construction. Apart from the production of single parts, recent years have seen a growing trend towards (small) series production runs. This trend is supported by a steadily increasing variety of available materials, processes and machines that are adapted to series production requirements.
The challenge of individual finishing
However, just like other manufacturing methods, additive manufacturing should never be viewed in isolation from the rest of the process chain. Several things have to be taken into consideration here, as Dr Andreas Mettenbörger, additive manufacturing specialist at LUKAS, explains: “Be it upstream processes such as the production and preparation of powders, or downstream processes like unpacking, de-powdering, removal of supporting structures or the fabrication of the final geometry and surface quality, new challenges have to be overcome at every step to ensure a structured production process.”
As an expert for surface finishing with many years’ experience in the fields of milling, grinding, polishing and cutting, LUKAS is also a competent and reliable partner for future-oriented and innovative technologies such as additive manufacturing, and offers a broad product range with solutions for many special scenarios. This is where Dr Andreas Mettenbörger sees the strengths of the tool manufacturer: “The LUKAS tool range is perfectly equipped for finishing 3D printed products of all types and shapes – regardless of the material. Our comprehensive product range offers the right solution for all finishing problem scenarios.”
Innovative tools as problem-solvers
“LUKAS diamond mounted points with an electroplated bond for rough surface finishing, for example, are ideally suited for a wide variety of metals and ceramics. Alongside a long tool life and good heat dissipation for “cool” grinding, they also offer good chip removal due to the large chip gaps,” says Dr Mettenbörger. “And special solutions in practically any geometry are naturally possible in addition to the standard programme.”
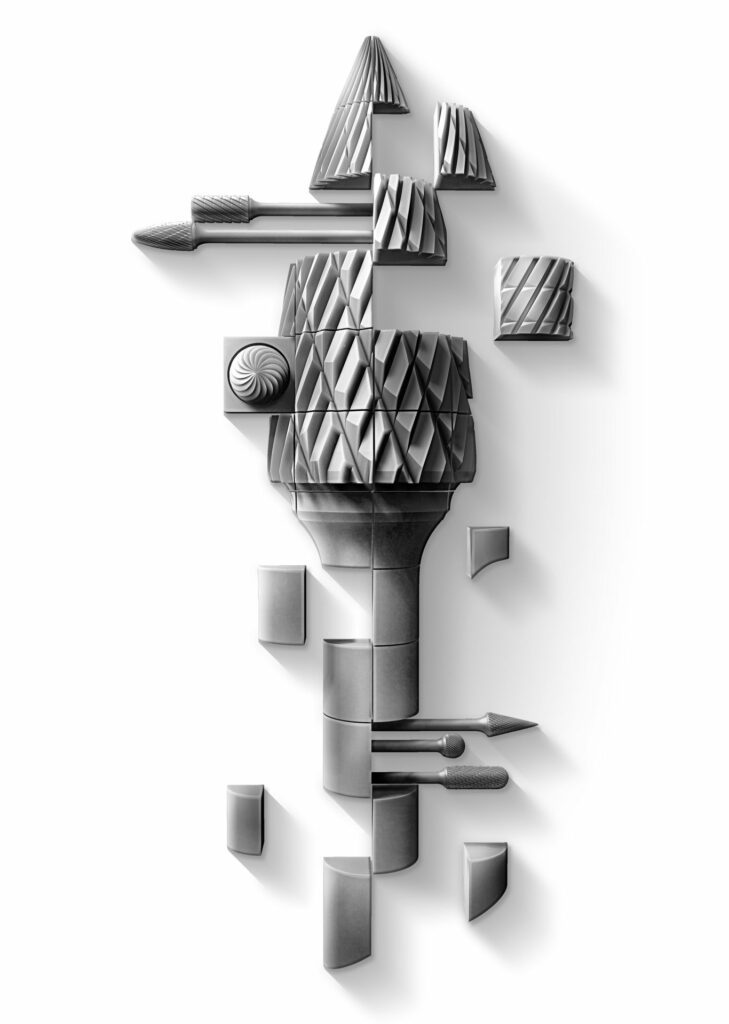
This also applies to many other products from the tool manufacturer’s product assortment: From diamond files with different profiles, mounted points for fine machining, to polishing tools for the final finish, the right tool solutions are available to overcome every challenge in additive manufacturing. In particular, the various burrs offered by LUKAS for rough processing metals have already proven their value in finishing 3D printed products. “These tools are ideally suited for removing supporting structures from many different materials,” says Dr Mettenbörger. “Just ask us to optimise your processes! Our technicians come directly from practical fields and have many years of in-depth user, production and industry knowledge. In addition, we collaborate directly with renowned 3D printing companies to optimise our tools even further for this specific application. We bring this knowledge straight to you and together we work out an individual solution.”
LUKAS – NEXT LEVEL SOLUTIONS.
As a technologically leading manufacturer of powerful and innovative milling, grinding, polishing and cutting tool solutions, LUKAS-ERZETT GmbH & Co. KG, based in the greater Cologne area, always focuses on the requirements of its customers and the latest developments in many different industries. AGILE, SUSTAINABLE, RELIABLE and FUTURE-ORIENTED – LUKAS thinks further, develops tailor-made solutions, and is always one step ahead of market requirements. This focus gave us the lead early on in the market and still does to this day.
All of the products that we manufacture and sell stand for outstanding quality characteristics such as powerful working, a long service life, excellent ergonomics and the very best results. If standard solutions don’t suit, we develop customised solutions to satisfy every application. This way, both your products and ours will always be ready for whatever the future holds.
LUKAS at the cutting edge of a global industry
With around 700 employees, state-of-the-art production sites in Germany, the Czech Republic and South Africa, a huge wealth of experience and a broad product range, LUKAS is firmly established in the markets. We are internationally active with branches and representatives on every continent. With over 80 years of experience, we produce system solutions for use in the automotive, aerospace, energy and construction industries, as well as for tradespeople.