Efficient tool for mould making: LUKAS-ERZETT sets standards
Mould making, an important area in tool and machine engineering, requires precise instruments to create complex structures and exact contours. Choosing the right tools is a decisive factor in order to be able to assure the highest quality and efficiency in the manufacture of casting moulds. LUKAS-ERZETT GmbH & Co. KG, a renowned player in the industry, offers a wide range of high-quality tools specially designed for mould making.
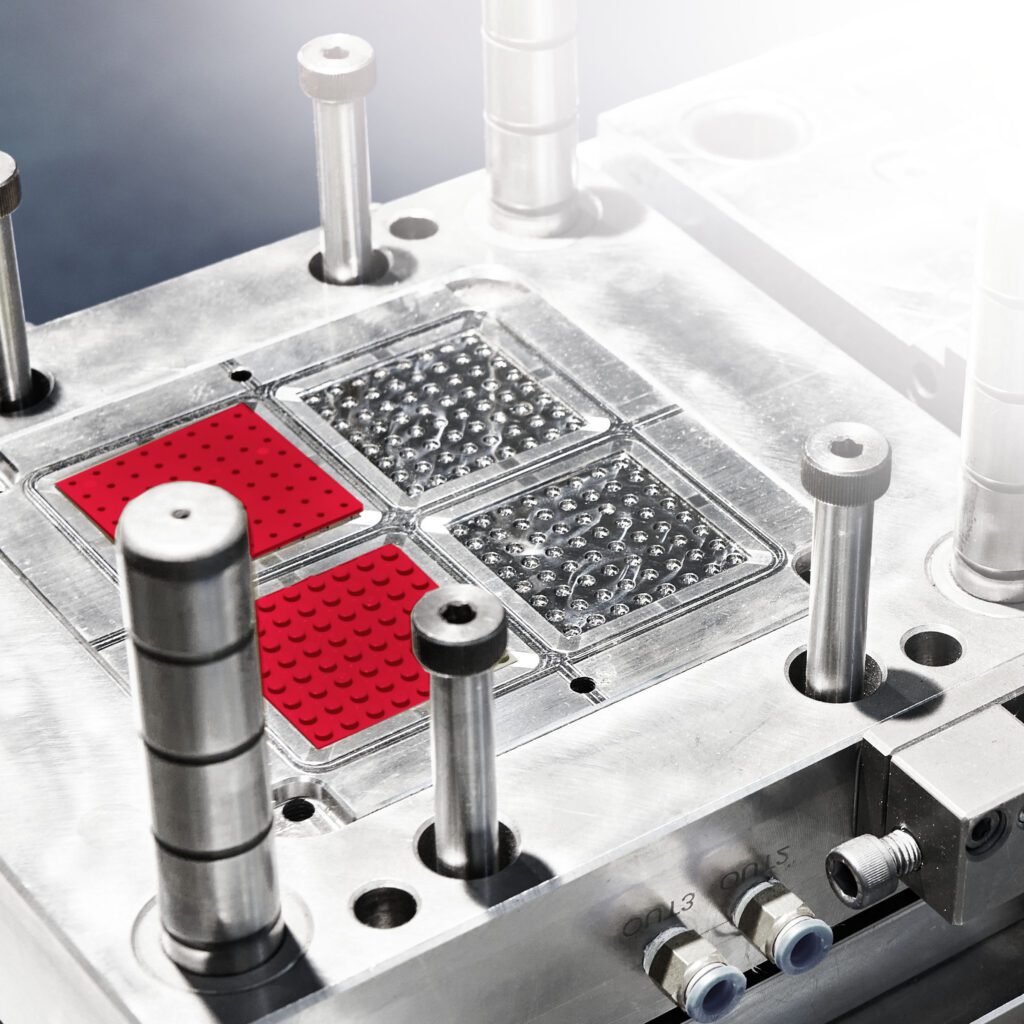
A mould always consists of at least two parts, usually divided into the nozzle side and the ejector side. Both halves together form the negative contour of the casting as a cavity. After the injection or casting and subsequent solidification of the casting, the machine moves the mould halves apart, whereby the moulded part remains in the ejector side and is ejected by a separate ejection mechanism. To optimise this process for the series production of identical components, exact precision of the moulds, as well as a perfectly polished surface of the negative contour, are of elementary importance in order to avoid faults and factory seconds during production.
Precision is the key in the manufacture of moulds for producing castings made of plastic, metal or glass. LUKAS-ERZETT presents a range of products that are ideally suited for fulfilling the requirements of mould making. Grinding and polishing tools from LUKAS are especially popular among toolmakers and mould builders.
LUKAS mounted points with ceramic grain (CER), for example, are suitable for effortlessly removing material and creating fine surfaces. These grind the hardest tool steels without any problems and in a particularly cool manner, and are ideally suited for quickly levelling repair grinds. The self-sharpening effect of the ceramic grain guarantees constant sharpness and cutting ability. The “NDW” small mounted points from LUKAS are suitable for extremely similar applications and stand out with their optimised aluminium oxide mixture for non-hardened and hardened tool steels. Their combination of abrasives with extremely tough and splintery grits ensures high removal rates and a good surface finish.
After the fine sanding comes the polishing. A critical and elementary factor in mould making is the surface quality – especially in the case of plastic castings. LUKAS offers a wide assortment of polishing tools especially designed for fine machining and polishing work. LUKAS polishing points, polishing discs, polishing sticks and polishing rollers, which, needless to say, are made of high-quality raw materials, enable the appropriate polishing finishes to be achieved for different applications. With the polishing tools from the P1 to P6 series, a surface can be optimised through to gloss and high-gloss polishing results.
Whether you just want to make your product shine properly or you need to achieve certain technical surface values for it, there are many good reasons for machining workpieces using polishing tools from LUKAS. In tool and mould making in particular, the mould surfaces are always polished to a mirror finish to achieve the perfect result on the end product with every casting. In glass manufacturing, for instance, final machining of the cavities often takes place using our proprietary high-quality LUKAS diamond pastes. Thanks to their extreme flexibility, P3 felt polishing points used together with LUKAS diamond paste are also ideally suited for polishing highly complex moulds such as pressure and injection moulds, or drawing, press and cutting tools, dies, bearings, spindles, etc.
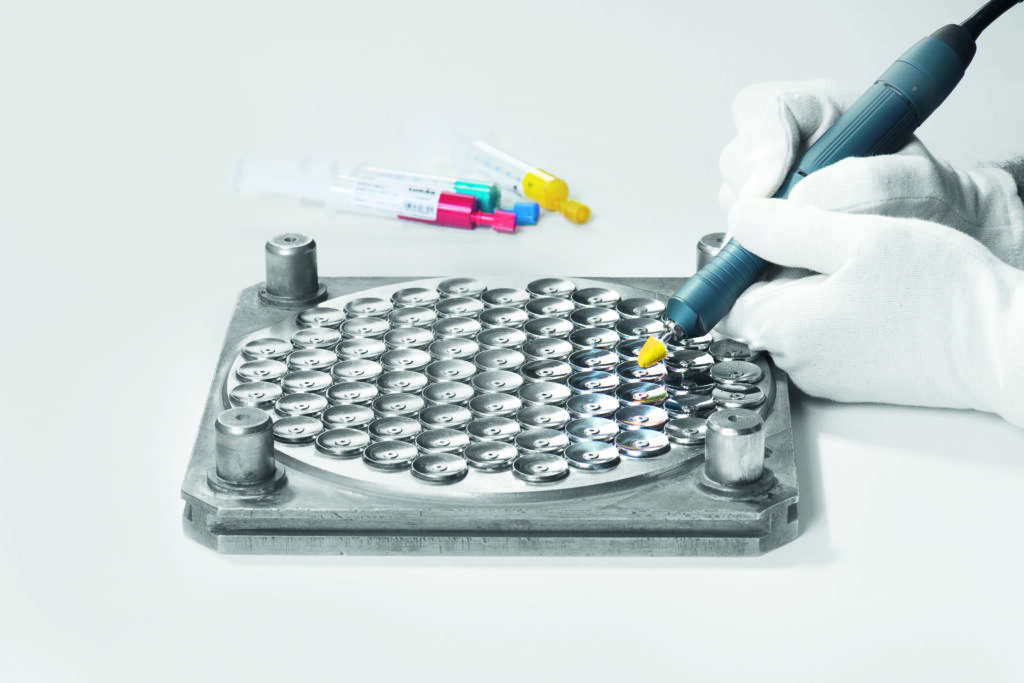
LUKAS-ERZETT is not only the polishing specialist, but also offers a wide range of other mould-making tools such as burrs, mounted points and flap discs.
Machining tools down to the narrowest tolerance ranges requires a hardness and strength adapted to the intended purpose. LUKAS grinding tools with a self-sharpening effect for tool and mould making are extremely dimensionally stable and can cut even the hardest materials. Due to its microcrystalline structure, the LUKAS ceramic abrasive cap is extremely friable and therefore self-sharpening. Worn abrasive particles break off, exposing new particles with sharp cutting edges. This is why the abrasive cap remains as sharp as new for a long time. Materials that are difficult to cut, such as hardened mould surfaces, can therefore be machined without any problems. Thanks to the self-sharpening effect, the tool life of a ceramic abrasive cap is many times longer than that of conventional abrasive caps. Tool changes are required much less frequently for straight grinders, reducing the tool costs. The comprehensive LUKAS product range allows you to reach and machine even the tightest areas.
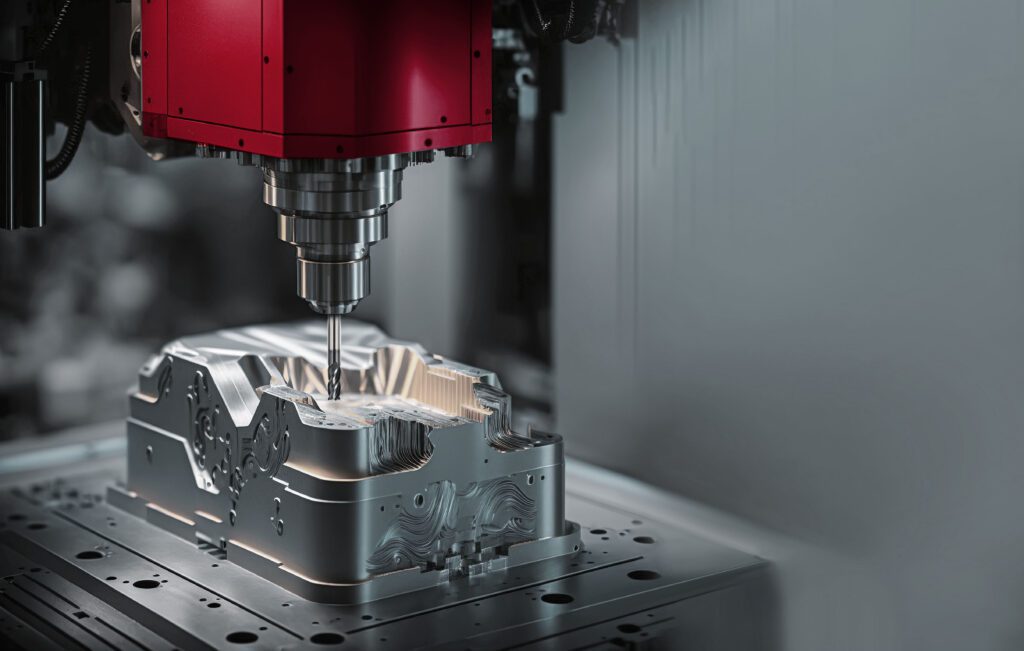
Away from mould making, tools of a particularly high hardness and precision are also required for stamping sheet metal and other materials. In high-performance stamping, progressive tools are made which cut, bead, rivet and form the sheet metal in several steps. Dabbing (also called spotting) is the final machining stage for large sheet metal stamping dies used in the automotive industry. The objective of this process is to produce a flat or uniformly curved surface and ensure consistent material thicknesses. Whetstones or sharpening stones are used for this purpose. Precision and a perfect surface finish are standard characteristics here. The specially developed LUKAS products are particularly suitable for such requirements due to their reliability and high grinding quality. So-called “pilot burrs” with an untoothed tip are very popular in tool and mould making because, when using them, no unintentional damage is caused to surfaces that have already been machined. At the same time, the tip can be used as a support point for precisely guiding the burr by hand.
Not only the quality of its tools, but also its comprehensive technical and expert knowledge make LUKAS-ERZETT stand out from other suppliers. The company’s experts understand the challenges of mould making and develop customised solutions. They advise the customers and help to find the most efficient tools for each step of their processes. This holistic approach not only guarantees optimum results, but also contributes to reducing scrap and increasing productivity in mould making.
In an industry that demands precision down to thousandths of a millimetre, high-quality tools are absolutely indispensable. LUKAS-ERZETT has established itself as a reliable partner for mould makers and supports the industry with innovative and high-performance solutions. The broad range of tools, combined with sound know-how, makes LUKAS-ERZETT the first choice for everyone who wants to achieve excellent results in tool and mould making. Visit the official website of LUKAS-ERZETT to learn more about their mould making products and services: https://lukas-erzett.com/de/branchenloesungen/werkzeug-und-formenbau/